What is a glycol loop?
Having an effective glycol cooling system is essential for keeping temperature control across your water, fermenting beer and the finished product. So, what are we talking here?
Well simply put, it is a closed loop system that runs cooled glycol around the jackets of your tanks, is warmed in the process and then returned to a chiller to be cooled before being pumped around again. But of course, nothing is that simple.
The effectiveness of this system impacted by several decisions — the size of the chiller, positioning of the chiller in your brewery layout, the piping material and the mix of glycol to water.
First, we need the glycol chiller that cools the mix of glycol and water to between -2°C to -4°C. Adding glycol to water allows the solution to flow below freezing temperatures. The size of the glycol chiller is determined by the number and size of the tanks needing temperature control, heat load, volume of glycol solution. PMG’s team of experts can help you to size your chiller and GWT for your current brewery’s efficiency as well as for future expansion plans.
As for piping for your glycol loop, stainless-steel is the best choice due to its aesthetics of matching the tanks, its corrosion resistance as well as ease of cleaning.
About these connections — each tank has a ball valve to control the supply and return of the glycol solution. This is where it gets interesting. In a circuit, the first vessel will get all the love: the coldest glycol at the highest flow rate. The further down the line, the glycol will be slightly warmer and slower.
By having ball valves at the junction to each tank, you can reduce flow into the vessels closest to your glycol chiller so that more (colder) solution reaches the tanks that are last in your loop. The valves can also be manipulated to reduce flow if your tanks are getting too cold or the there are any signs of freezing in the jackets.
The positioning of your chiller within your brewery layout is also important. This unit produces a lot of heat itself so adequate airflow around the unit is recommended. There is also consideration that bends in the piping system reduces pressure – so designing the positioning to minimise the number of bends and fittings in the circuit can help to maintain pressure.
Now the mix of glycol to water. The essential consideration here is the glycol burst protection level. This must be significantly lower than your lowest anticipated environmental temperature. Pure water freezes at 0°C. Operating with a 35% glycol to 65% water solution typically will protect from freeze up to -17°C. At this temperature the system will be protected, the coolant will become slushy but able to flow into a glycol water tank. This is very important for closed loop systems exposed to freezing conditions.
The proper glycol to water ratio mixture is very important in your chiller system. Too little glycol can lead to a costly freeze up in the unit — too much glycol can reduce your systems efficiency.
Having an effective glycol cooling system is pivotal to producing consistent quality beer. Our design and engineering team here at PMG will help you to design the best and most efficient layout of your tanks for total control at all steps of the production cycle. PMG can provide every component you need in your loop; glycol chiller, cellar temperature control unit, tank farm (GWT, CLT, fermenters, unitanks, brites) and all the piping, valves, fittings and pumps.
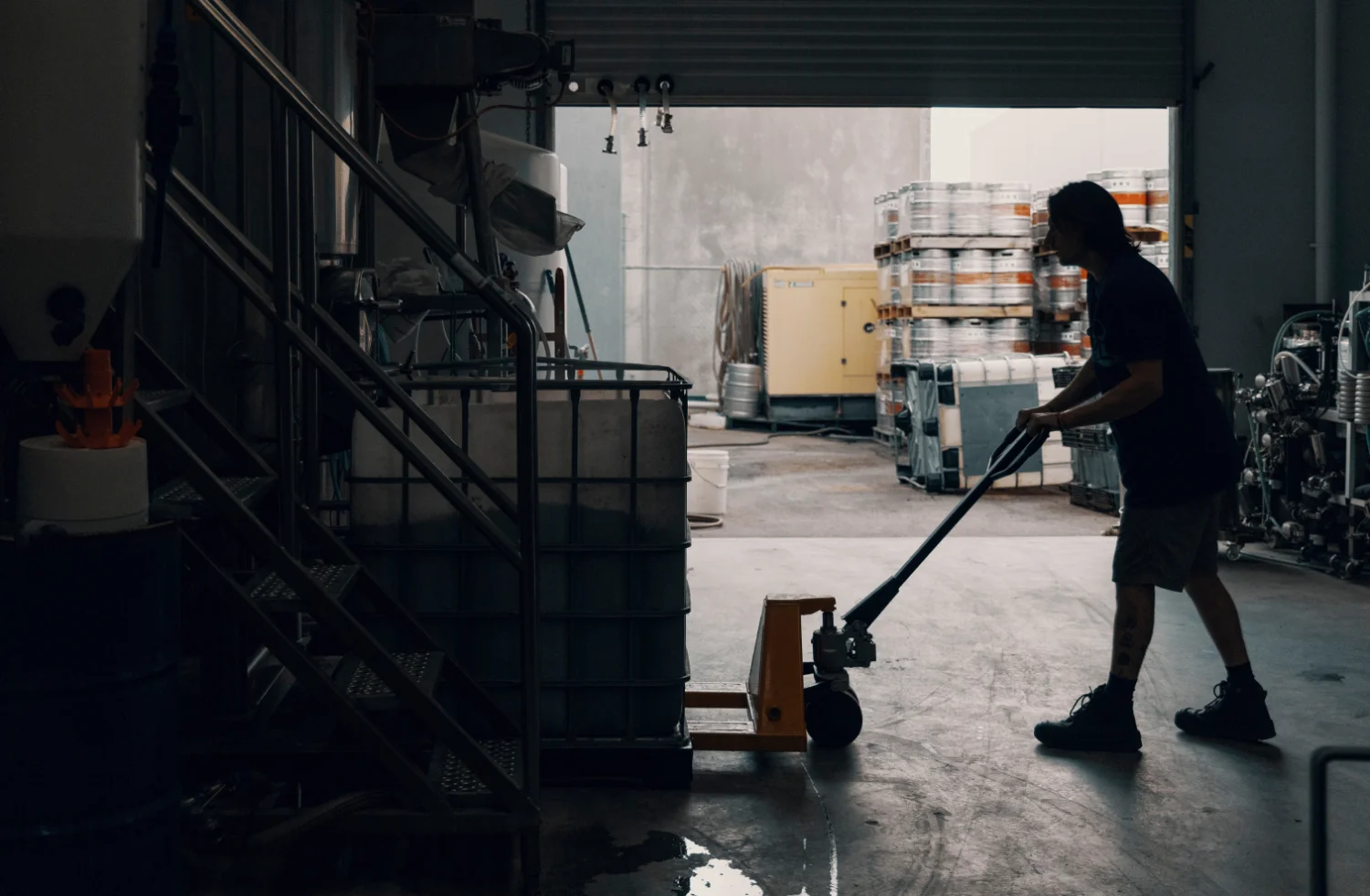
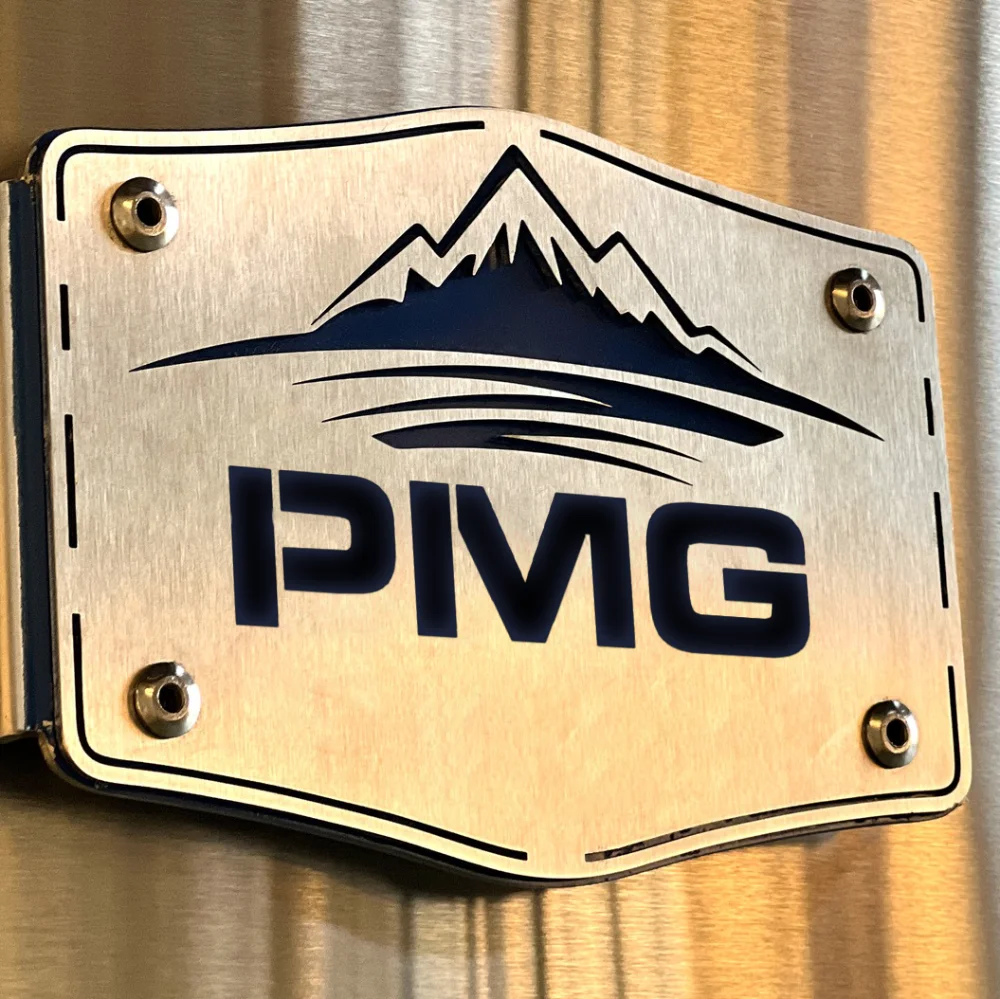