The difference between Brite and Unitanks
Brite tanks mark the final stage of the brewing process, following the journey from the brewhouse and fermenters. They serve dual roles, acting as storage vessels for finished beer destined for canning, bottling, or kegging, while also functioning as serving vessels for direct pouring in taprooms or brewpubs.
Unitanks merge fermenter and brite tank features, offering brewers the convenience of fermenting or carbonating beer in a single vessel. This versatility is particularly attractive to brewers seeking flexibility in their cellar operations.
The multi-functionality of unitanks makes them a preferred choice for some craft breweries, minimizing the need for additional costly equipment and freeing up floor space or reducing the number of tanks in your glycol loop. With only one tank required, beer movement is streamlined, reducing both time and effort. Additionally, unitanks can cut down on expenses associated with separate equipment, serving as efficient all-in-one solutions.
Contamination risk from airborne organisms is a critical concern in brewing, with oxygen exposure posing a constant threat. Unitanks mitigate this risk by safeguarding beer from air and bacteria during transfer, ultimately reducing labour requirements and supporting smaller breweries.
However, brite tanks offer distinct advantages as well. Transferring beer from a secondary tank into a brite tank post-fermentation yields clearer beer, especially when yeast is filtered out beforehand. Breweries often favour this clarity-enhancing process for aging beer, commonly conducted in brite tanks.
In summary, larger breweries may find brite tanks more beneficial, whereas microbreweries and smaller operations typically derive greater value from unitanks. Brewers should carefully weigh these factors when choosing between brite tanks and unitanks.
So, we have reached the end of the brewing process — and yet there are still decisions to be made. Where should we store this beer, either to finish fermenting or to mature, a brite tank or unitank?
A brite tank serves a couple of roles, acting as storage vessels for finished beer destined for canning, bottling, or kegging, while also functioning as serving vessels for direct pouring in taprooms or brewpubs. Traditionally, it served as a container for maturation following primary fermentation.
The major difference between a brite and unitank is the shape of the bottom. Unitanks has a conical shape to allow the yeast to accumulate. This allows a unitank to function as the fermenter and allow for carbonation in the same vessel — beer can be fermented, matured, purified, and carbonated in one tank.
This seems like an easy decision — using one vessel allows streamlining of beer movement, mitigation of potential oxygen exposure and ultimately reducing time and effort. With less equipment costs, and with scheduling you can produce more types of beer in fewer tanks.
But … always a but… brite tanks, the clue is in the title, offer distinct advantages in transferring from a secondary tank to yield clearer beer, especially by filtering the yeast. Brite tanks, usually at a 5° angle, occupy less space per volume and not as expensive as a unitank.
In terms of production, dividing brewing and packaging as two separate operations, in two areas of the brewery floor has advantages, not least of all to free up the fermentation tank for the next batch of beer. So, for larger scale operations, brite tanks holding more liquid in them, are considered the better option. Unitanks, when space is limited or in a brewpub setting where focus is less about packaging and more on serving the beer then and there, seem to be preferred.
Many brewers are inclined to have a brite tank regardless — as a back stop to assist in clarity for those difficult beers, to ensure a proper homogenous mix particularly if adding adjuncts and to free up fermenters.
Like all equipment decisions, PMG will not only supply you with options but with professional drawings of our equipment in your brewery so you can make the best decision on how to most effectively and efficiently use of your space.
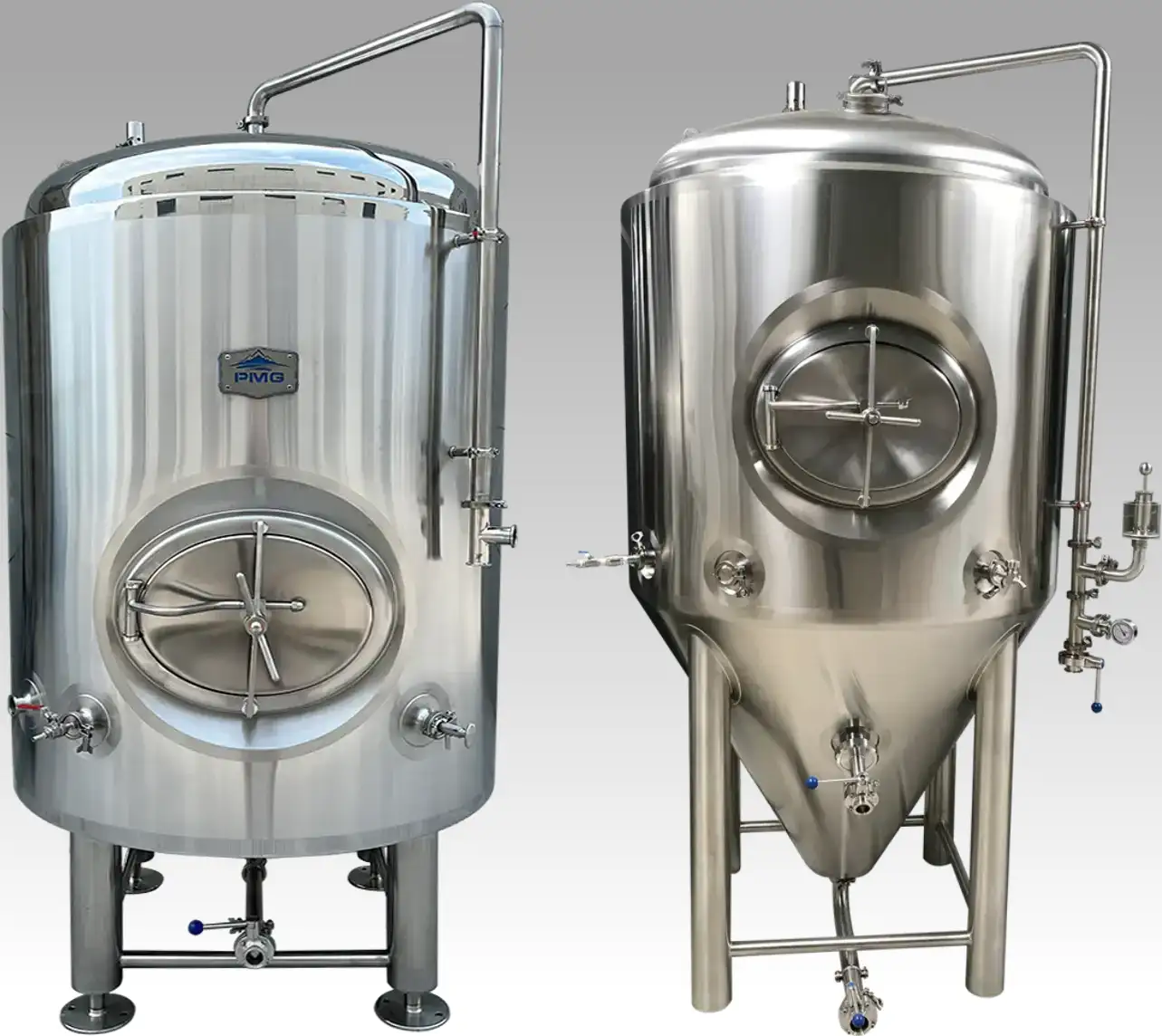
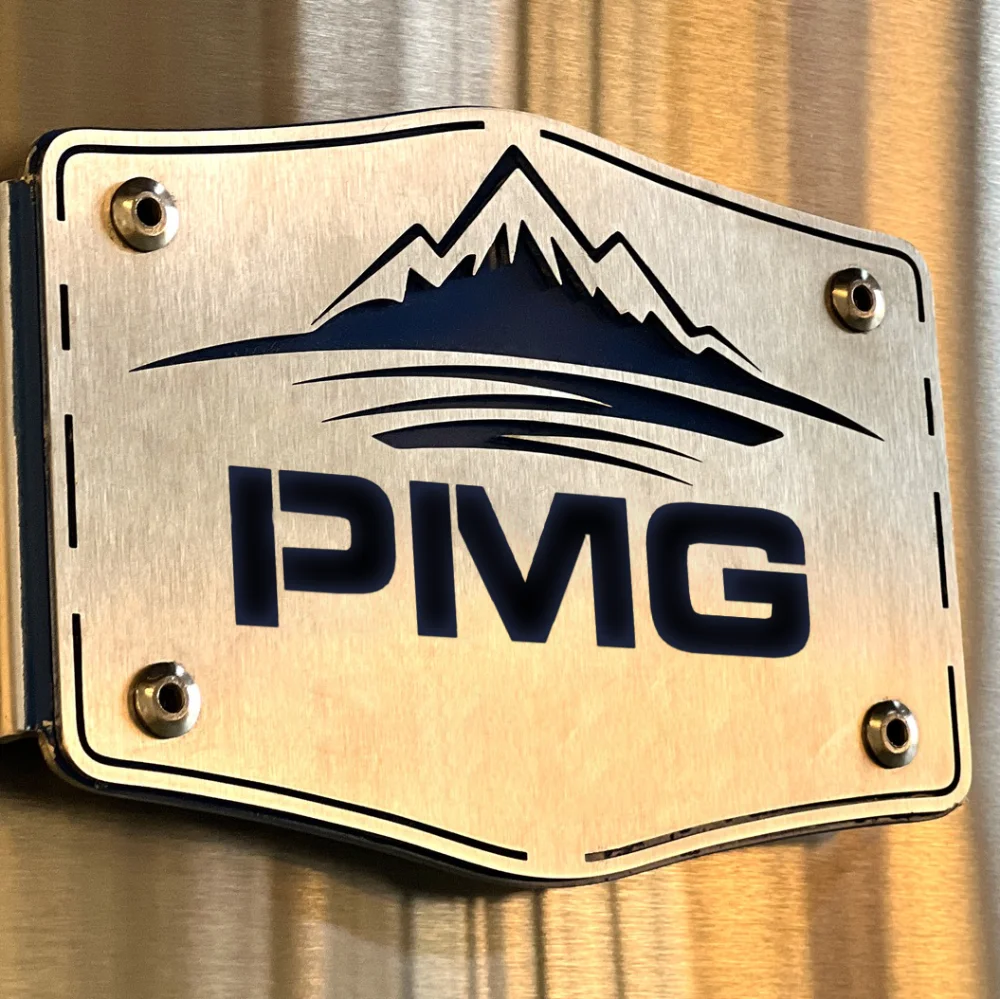